CIPP lining, or Cured-in-Place Pipe lining, is a trenchless method used to repair existing pipelines. This technique involves inserting a resin-saturated liner into a damaged pipe. The liner is then inflated and cured in place using hot water, steam, UV or blue LED light, forming a new, durable pipe within the old one. This process is minimally invasive, requiring little to no digging, and is commonly used for sewer, water, and gas pipelines. CIPP lining is valued for its efficiency, cost-effectiveness, and ability to extend the lifespan of existing infrastructure without extensive disruption.
CIPP repair methods have been around since first introduced in 1971 in the UK by Eric Wood, an agricultural engineer. Needing to fix an air duct over a mushroom bed, which entailed dealing with 230 feet of pipes, Wood came up with a trenchless solution. Pulling epoxy or resin saturated felt liner through the damaged pipeline, the liner would then be expanded using air to fit the contours of the pipe. The adhesive will then “cure” or harden.
Comparing CIPP Methods
Being a relatively new technology, and an elegant solution to a common problem, the method has remained relatively the same to Wood’s original idea. But with the need to create a more sustainable future, and maintain compliance with the ever changing landscape of modern regulatory frameworks, the technology behind the solution has evolved. Traditional methods of curing the pipe lining have involved ambient, hot water or steam cured methods. While they do the job to a certain extent, and are still a far more efficient option to excavating pipes for repair, they do have a number of drawbacks.
Ambient
Slow to cure
Small operational footprint
Minimally disruptive
No special equipment
Low cost
Limited to small sections
Hot Water
Reasonably quick
Large operational footprint
More disruptive
Large specialist equipment
High initial costs
Suitable for larger pipes
Steam
Reasonably quick
Medium operational footprint
More disruptive
Specialist equipment
Medium initial costs
Higher safety concerns
UV (Bulb)
Quick to cure
Large operational footprint
More disruptive
Higher initial and long-term costs
Suitable for very large pipes
No use on bends
UV (LED)
Very quick cure
Medium operational footprint
Low disruption
High initial costs
Low long-term costs
Suitable for very large pipes
Bluelight LED
Almost instant cure
Low operational footprint
Low disruption
High initial costs
Low long-term costs
Repairs last 50+ years
Ambient methods, which involve allowing the resin to cure naturally, meant engineers could not wet out the lining off site as it would harden between creation and inversion. This means adding the resin to the liner in the field, and it is only recommended for short lengths of repairs. Although the ambient method has a low footprint, it is a longer process.
Hot water curing, known as hot cure, involves pumping water heated to 80° through the lined pipe to cure the resin. The lining can be impregnated before delivery, usually via refrigerated transport, and is a lot faster than ambient methods. However, the need for a water boiler along with a vacuum tanker to remove the water from the system after curing means the method requires a large footprint to operate in.
The steam curing method also has the liner impregnated before delivery to site, and requires less water supply. It does not require the use of a vacuum tank to remove water afterwards, so it enjoys the faster curing time without the large footprint. The drawbacks however are the risk of cold spots within the pipe during the curing process, meaning the risk of weakness in the pipe wall. Steam generation also requires a larger compressor for hot cure methods, and a more stringent safety process due to the large amount of hot steam being emitted from the boiler.
These more traditional CIPP methods all have their problems, especially with operational footprint, noise, emissions and fumes which can disrupt the surrounding area. Furthermore, there is the risk of over- or under-curing the liner, potentially causing additional damage or subpar repairs.
As a result, contractors are increasingly seeing the benefits of light-cured lateral CIPP solutions. These produce no emissions and are a much quieter process, making it both a more environmentally sound and less disruptive option. They can also be precisely controlled with light-curing equipment, ensuring the liner is cured evenly and thoroughly. This results in a more accurate and effective repair. Light-cured CIPP uses one of two light wavelengths to quickly harden the resin: Ultra Violet (UV) and Blue light.
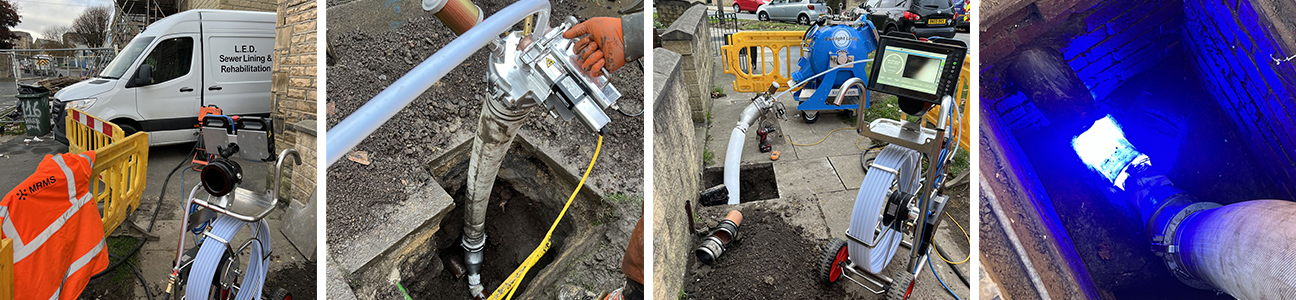
UV cure was developed in the 1990’s and uses UV liners which can be available at larger diameters. The method is quick to cure and produces a high strength wall. The liner is pulled by winch through the pipe and then UV lights are run through the pipe to initiate the cure. The UV light bulbs are filament and have a limited lifespan, so need replacing. It is a time-consuming setup with a large operational footprint needed due to the equipment required, including larger compressors and generators than for traditional methods. It is also not possible to use it in a pipe section with a bend.
Further advancements in UV technology led to the UV LED method, bringing with it the advantages of UV curing in a much smaller package. Using LED instead of filament bulbs means fewer power and energy requirements, so the operational footprint is greatly reduced, as is the potential impact on the surrounding environment. However, UV has a wide wavelength range with a lower intensity than other wavelengths. This can lead to issues penetrating the resin, causing an incomplete cure. As such, the lining material usually incorporates glass fibres and a reflective outer foil in order to reflect UV back onto the resin layer and assist the cure.
The Bluelight System
Bluelight LED was first developed in Denmark in 2008. The diodes emit blue light, which has a very short wavelength range and much increased intensity than UV light. This allows for a deeper and more complete cure and doesn’t rely on specific lining materials to help it cure the resin.
The Bluelight system uses a resin that only hardens when exposed to blue light. This significantly increases the time operators have between the wetting out process and inversion into the pipes, decreasing the risk of hardening before inversion. It also greatly reduces the time it takes to cure the pipe lining when inverted, up to five times faster than other methods.
The curing system pulls the LED head through the installed liner, curing the resin almost instantly – a 50-foot sewer line could be fully cured in under 10 minutes using this method.
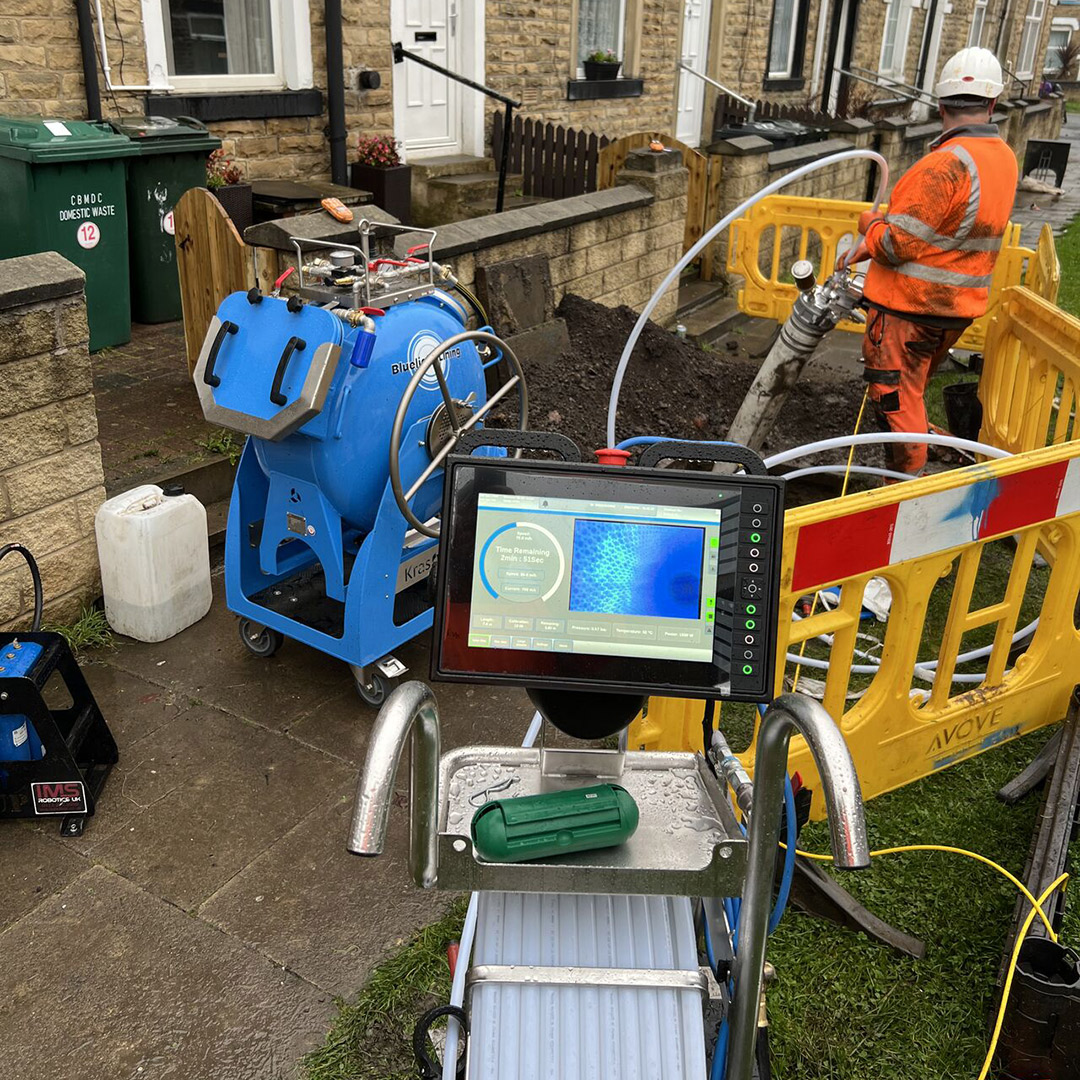
MRMS has invested in a dedicated CIPP system from Bluelight Lining Ltd, and is capable of installing and curing liners from DN100 – DN500 in lengths of 100m+. The system is installed in a specially converted Mercedes Sprinter, which also includes safety equipment, a workbench, storage racking and a rear loading ramp. The stability, efficiency and speed of using the Bluelight Lining system means planners, architects and building owners can enjoy many benefits:
- Quick and reliable project management
- Proven process safety
- Long-term compliance with drainage regulations
- Minimal disruption
- Long-lasting, cost-effective repairs
Contact Us About Our Bluelight System Repair Services
Call 01274 050137 • Email info@mrms.co.uk