This summer, Yorkshire has officially entered drought status, following an unseasonably dry winter and spring. While the immediate effects, such as restrictions on water usage and environmental pressures, are widely reported, there is less public discussion on how drought conditions affect critical infrastructure, particularly sewer and drainage systems in commercial and public sector environments.
For Tier 1 contractors, water utilities, and private estate managers, drought poses operational risks that extend far beyond water scarcity. These risks include increased asset strain, system integrity challenges, and maintenance complications that can compromise efficiency, safety, and compliance across complex drainage networks. Mitigating drought-related risks requires proactive drainage inspection, repair and maintenance services, if costly emergencies are to be avoided.
The Threat of Pipe Displacement and Failure
Extended dry periods reduce moisture levels in the ground, causing soil shrinkage, particularly in clay-rich regions common across Yorkshire. As the ground contracts, subsidence can occur, leading to pipe misalignment, joint displacement, or cracking in below-ground assets. These faults can result in leakage, blockages from the infiltration of debris, and, in extreme cases, system collapse.
Using precision CCTV drain surveys and GPS utility mapping, MRMS identifies vulnerable pipe sections before failure occurs. Targeted no-dig repairs, such as CIPP lining, prevent costly excavations and business disruption for industrial and public clients.
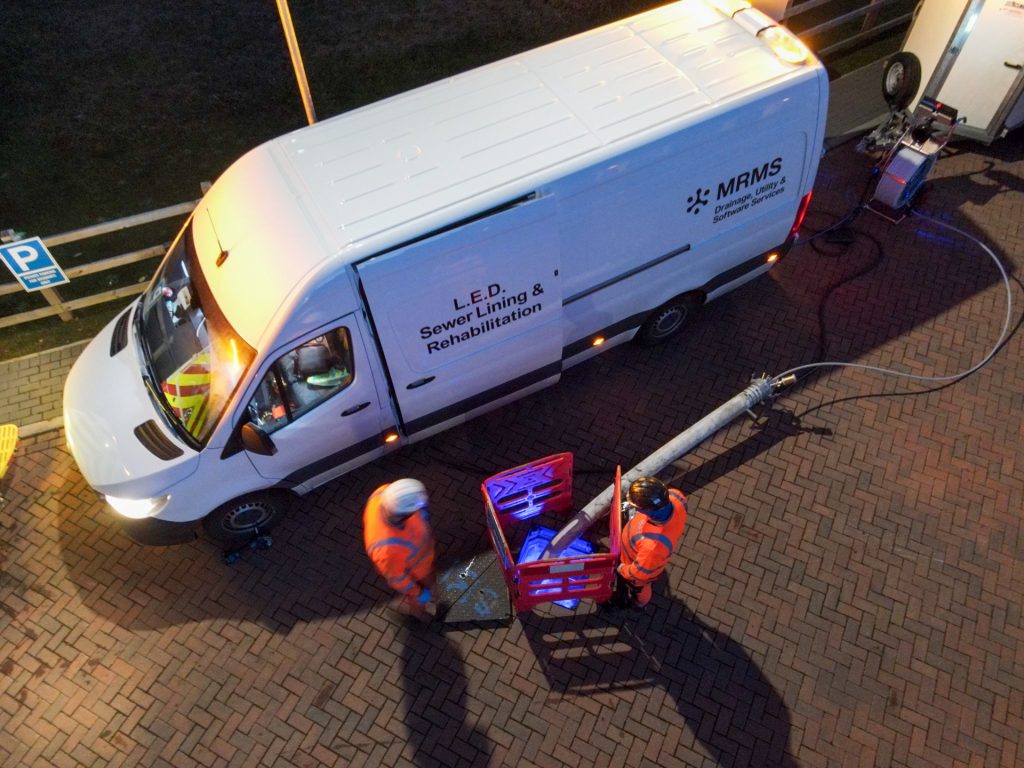
Slower Flows: A Growing Problem During Drought
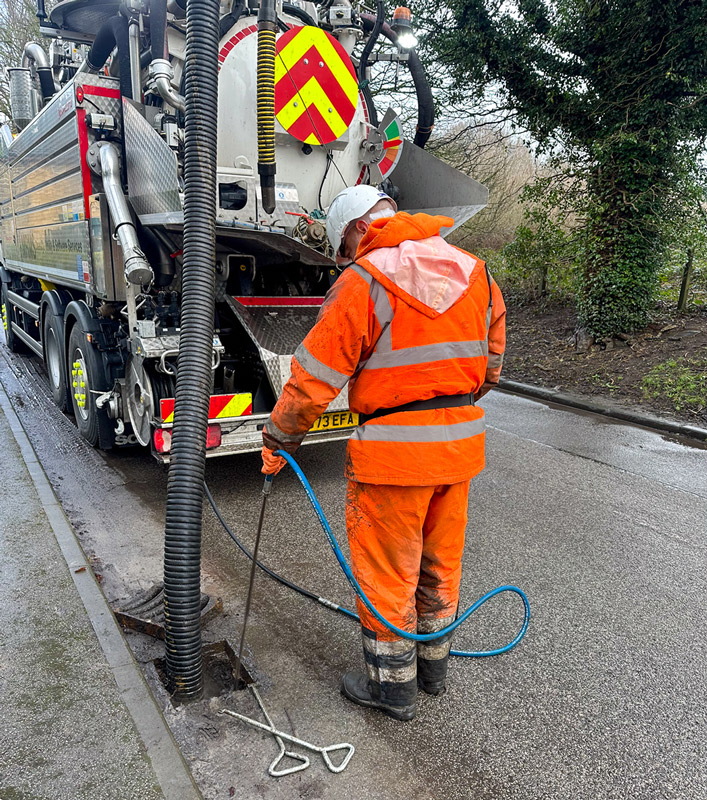
In commercial and public sector drainage systems, reduced water throughput during drought conditions can cause solids, fats, oils, and greases (FOG) to accumulate. This is particularly problematic in facilities such as food production plants, petrol stations and garages, where FOG production remains constant, but flushing volumes decrease.
Stagnant flows also encourage silt and debris buildup in surface water drainage systems, raising flood risks during sudden rain events, a known problem in industrial parks and retail zones with large impermeable surfaces.
Lower flow rates in commercial drainage systems reduce the natural flushing of gases and waste residues. This stagnation causes foul odours, an issue for premises such as hotels, offices, and public buildings where reputation and user experience are critical.
Regular high-pressure water jetting, vacuum tanker removal, and interceptor cleaning form part of MRMS’s preventative maintenance programmes. These services protect sites from operational disruptions and compliance risks linked to environmental discharge standards.
From Drought to Downpour: Flooding and Infiltration
Ironically, one of the most damaging phases occurs when droughts break. Parched and fractured ground can allow sudden surges of groundwater to infiltrate foul and surface water systems through damaged pipe joints or cracks, leading to sewer surcharge, pollution incidents, or asset overload. This presents compliance risks for both private operators and water companies, and is especially dangerous for hospitals, transport hubs, and sensitive industrial operations.
Scheduled pre-rainfall inspections can mitigate these risks cost-effectively. With our CCTV drainage surveys and condition assessments, MRMS identifies system vulnerabilities before wet weather returns. Repairs such as cured-in-place pipe (CIPP) lining can reinforce pipes against infiltration without costly replacement.
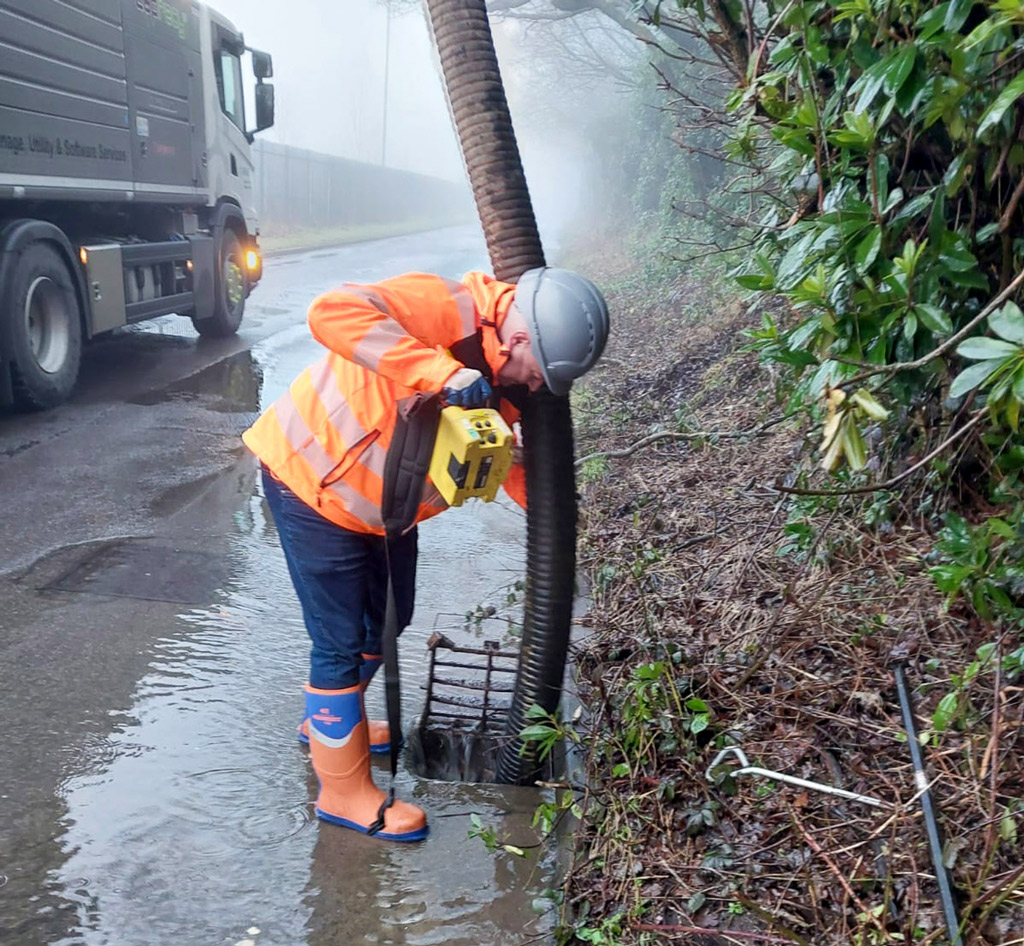
Preparing Drainage Infrastructure for Climate Uncertainty
With climate models predicting more frequent and intense drought cycles in the UK, these issues are likely to become recurring challenges for infrastructure managers. Yorkshire’s 2025 drought underscores the need for preventative drainage maintenance across commercial, industrial, and public sector infrastructure. MRMS supports this need through:
Asset Condition Mapping: Detailed GPS surveys and defect coding for predictive maintenance planning.
Non-Destructive Repair Techniques: Minimising operational disruption on high-footfall or critical sites.
Bespoke PPM Contracts: Tailored for any industry or site to ensure continuous operations, minimising the risk of costly emergencies.
Contact MRMS About Asset Management Solutions
Call 01274 050137 • Email info@mrms.co.uk